How are phone cases manufactured by injection molding?
Table of Contents
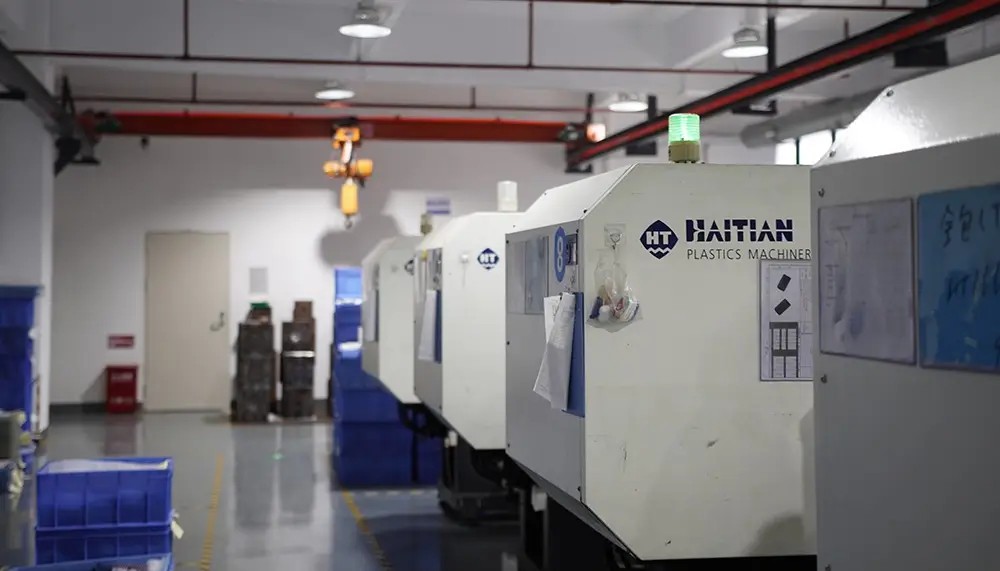
Introduction
There are many ways to make mobile phone cases, and no matter which one, injection molding is indispensable. Injection molding is the mainstream method of making mobile phone cases. In this article, we will detail how to produce mobile phone cases through injection molding, the key points and precautions of injection molding production.
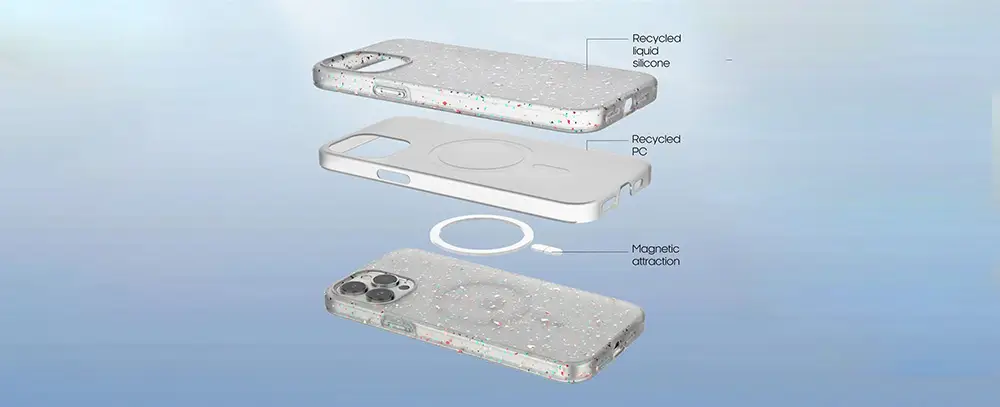
Prototype design
Before the project starts, we will design a prototype of the phone case: based on different phone case models and different functions, we will design prototype drawings. Most of the data comes from the technical documents of various brands. If there is no data, we need to test it ourselves. Use current mainstream materials as much as possible to design mobile phone cases.

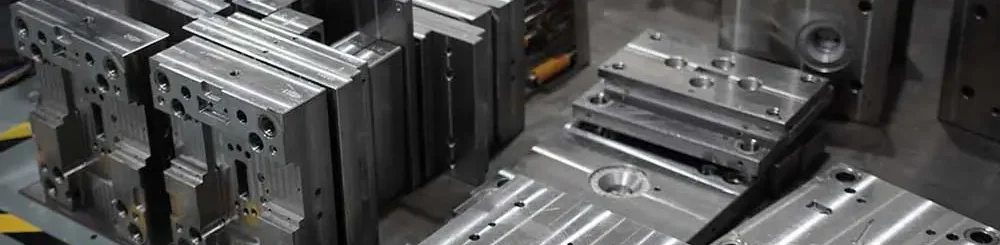
Prepare the appropriate mold
In injection molding, the mold is an important part that determines the appearance of the product. So when the phone case design is completed, we will design the corresponding mold according to the data of the phone case, and create a suitable mold according to the design drawings.
Pre-manufacturing
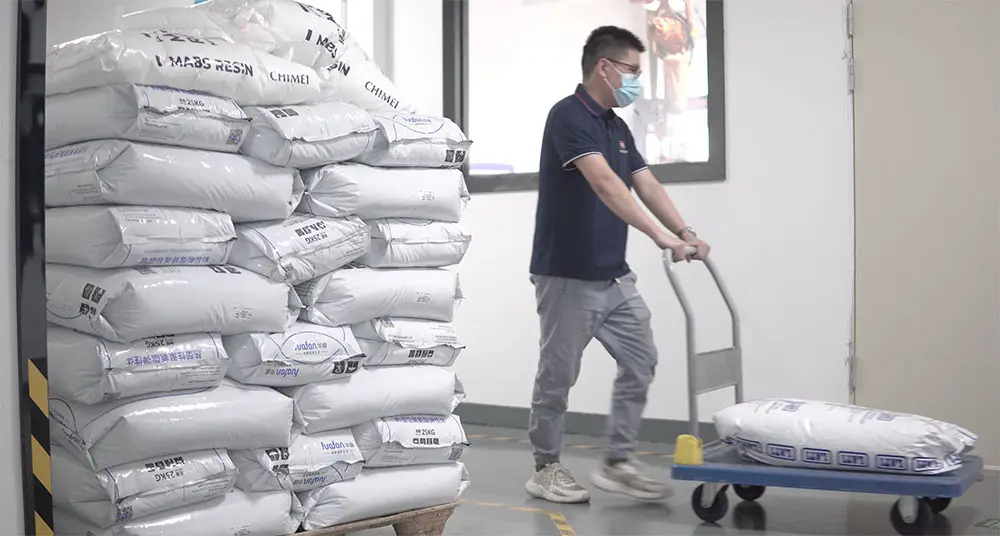
Material selection and pre-treatment
Commonly used materials:
Material | Characteristics | Applicable scenes |
PC (Polycarbonate) | High transparency and impact resistance | Transparent hard case |
TPU (Thermoplastic Polyurethane) | Soft and drop-proof, easy to color | Soft/anti-slip case |
ABS+PC hybrid | Combines strength and toughness | Functional thick shell |
TPU+PC hybrid | Compatible with clear and drop-proof | Printed case |
Pre-treatment:
- Granules need to be oven dried at 80-100°C for 4 hours (to avoid injection bubbles).
- Add color masterbatch or functional masterbatch (e.g. anti-UV agent, anti-fingerprint coating precursor).
Installation and commissioning of molds
1, Install the mold into the injection molding machine and adjust the clamping force (usually 80-150 tons).
2, Setting up the mold temperature machine:
- PC material: mold temperature 80-100℃ (reduce internal stress).
- TPU material: mold temperature 30-50℃ (to prevent sticking to the mold).
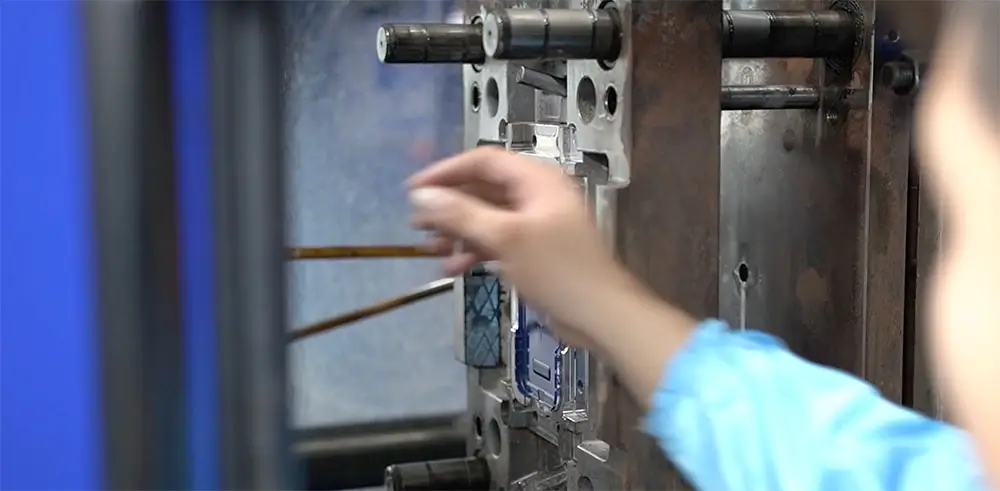
Injection Molding Core Processes
The core process of injection molding is divided into five steps, which are:
- Molding
- Melt injection
- Pressurization and cooling
- Mold opening and ejection
- Post-processing
Melt injection
Barrel temperature (segmented control):
- PC: 260-300°C (back section → front section increasing).
- TPU: 180-220°C.
Injection pressure: 60-120MPa, medium speed (to prevent jet lines).
Pressurization and cooling
Holding pressure stage:
- Pressure is 50-80% of injection pressure for 5-15 seconds to compensate for shrinkage.
Cooling time:
- Adjusted according to meat thickness (1mm thickness takes about 10 seconds, 3mm takes 30 seconds).
- Use in-mold cooling water circuit (water temperature 25°C ± 2°C).
Mold opening and ejection
The speed of the ejector is gentle (to prevent deformation of the top white), and the TPU shell needs to be sprayed with mold release agent in advance.
Post-treatment process
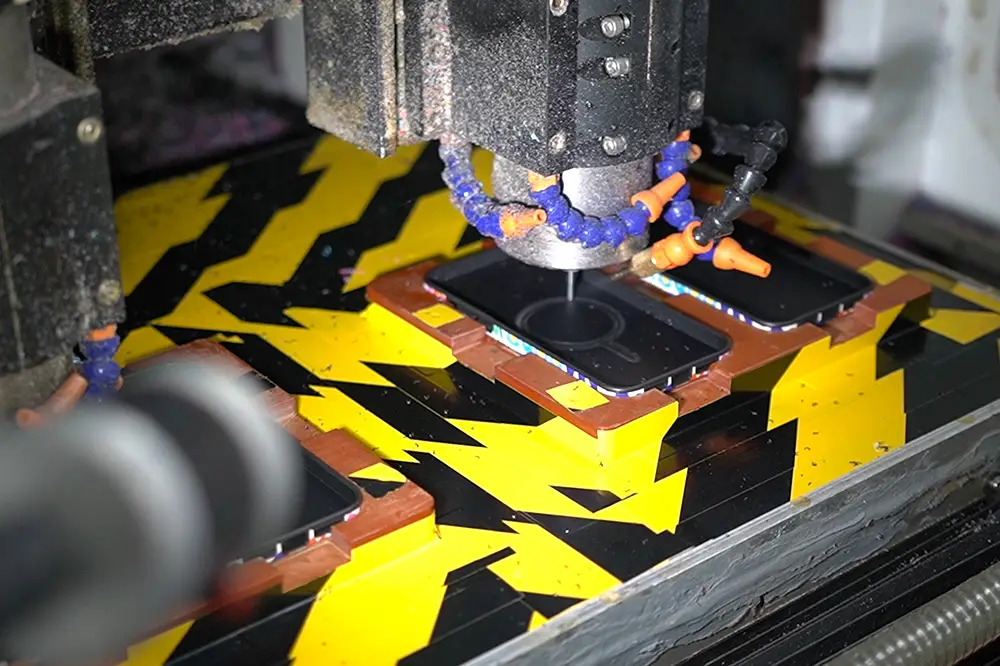
Remove excess material
- Manually or robotically cut away the sprue residue (spot gates need to be smoothed with a hot cutter).
surface treatment
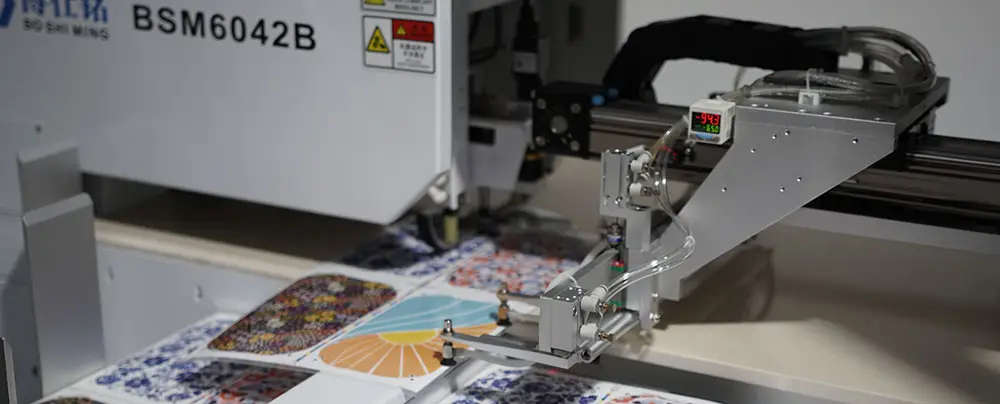
Spraying: UV coating (anti-scratch), hand feeling oil (skin-like texture).
Printing:
- Silk-screen printing (Logo/Pattern) → Positioning jig is required to ensure ±0.1mm accuracy.
- IMD (In-mold transfer) → Decoration is done directly in the mold.
Assembly & Quality Control
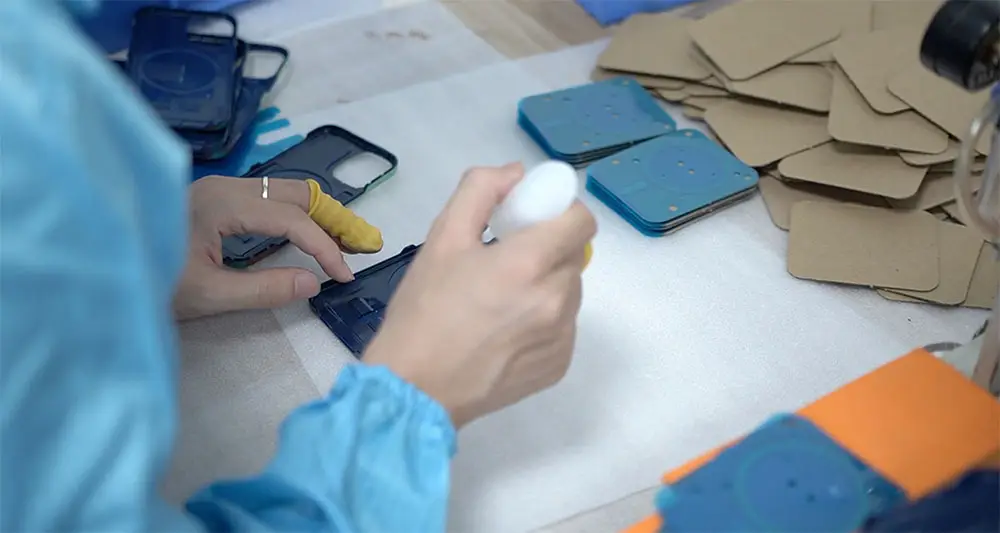
- Magnetic fittings, brackets, etc. are fixed by ultrasonic welding or glue.
- Full inspection items: size (caliper measurement), light transmittance (haze meter), drop test (1.5m concrete floor for 3 times).
At this point, a complete mobile phone case production process is over.
Key Parameter Control
Parameter | typical value for PC transparent case | typical value for TPU soft case | Consequences of loss of control |
Cylinder temperature | 280°C | 200°C | Decomposition discoloration/underfill |
Mold temperature | 90°C | 40°C | Stress cracking/surface rippling |
Holding time: | 12 sec | 8 sec | Shrinkage / oversize |
Cooling time | 25 sec | 15 sec | Deformation/mold sticking |
Common Problems and Solutions
Cell phone case surface bubble/silver pattern
- Reason: The material is not dried or the temperature is too high to evaporate gas.
- Countermeasure: Extend the drying time and reduce the temperature of the back section of the cylinder.
Cell phone case seam fusion marks
- Cause: Too fast cooling at the intersection of multiple melt strands.
- Countermeasure: Increase the mold temperature, increase the injection speed or modify the gate position.
Ejector Marks
- Cause: Excessive ejection resistance or insufficient cooling.
- Countermeasure: Increase the tilt of mold release, reduce the ejection speed or prolong the cooling time.
Conclusion
The above are all the details and key points of mobile phone case manufacturing through injection molding.
One Response